Changing Visions into Truth: Aluminum Casting Illinois
Changing Visions into Truth: Aluminum Casting Illinois
Blog Article
The Ultimate Light Weight Aluminum Casting Guidebook: Step-by-Step Instructions for Success

Safety Preventative Measures for Light Weight Aluminum Casting

Additionally, maintaining a neat work area totally free of mess can stop tripping threats and assist in the movement of workers throughout casting processes. aluminum casting illinois. Proper training in dealing with liquified aluminum and operating casting tools is vital to minimize the danger of accidents and injuries. Normal equipment maintenance and examination ought to be conducted to determine and remedy any prospective safety and security hazards immediately
Establishing Your Aluminum Casting Office
Developing a safe and effective office for light weight aluminum spreading is important for guaranteeing smooth procedures and minimizing potential risks. Before establishing up your work space, ensure that it is well-ventilated to avoid the buildup of harmful fumes produced during the casting process. Arrange your devices and tools in a sensible fashion, maintaining them within very easy reach however also maintaining clear paths for activity around the workspace. It is important to have a marked location for each and every phase of the spreading procedure, such as pattern making, mold and mildew prep work, and steel pouring, to enhance process and stop cross-contamination. Furthermore, make certain that your work space is outfitted with fire extinguishers and emergency situation security devices, and that all personnel are educated in correct safety and security treatments. Make use of heat-resistant materials for job surfaces and flooring to prevent damages and crashes as a result of high temperature levels. By carefully setting and planning up your light weight aluminum casting office, you can create an efficient setting that focuses on safety and security and effectiveness.
Choosing the Right Aluminum Alloy
To make certain ideal spreading results in your safety-focused and well-organized office, choosing the suitable light weight aluminum alloy is critical. Various light weight aluminum alloys offer different qualities such as toughness, longevity, heat resistance, and machinability. The option of alloy relies on the particular needs of your spreading project.
One frequently made use of aluminum alloy for casting is A356. This alloy displays excellent fluidness, making it perfect for complex spreadings with thin walls. A356 likewise has excellent corrosion resistance and mechanical homes, making it ideal for a variety of applications.
If higher stamina is required, 7075 aluminum alloy is a preferred option. Known for its high strength-to-weight proportion, 7075 is commonly made use of in applications where strength is essential, such as aerospace elements.
For jobs that include high-temperature atmospheres, 319 aluminum alloy is a great choice because have a peek at this site of its premium thermal conductivity and resistance to thermal fracturing.
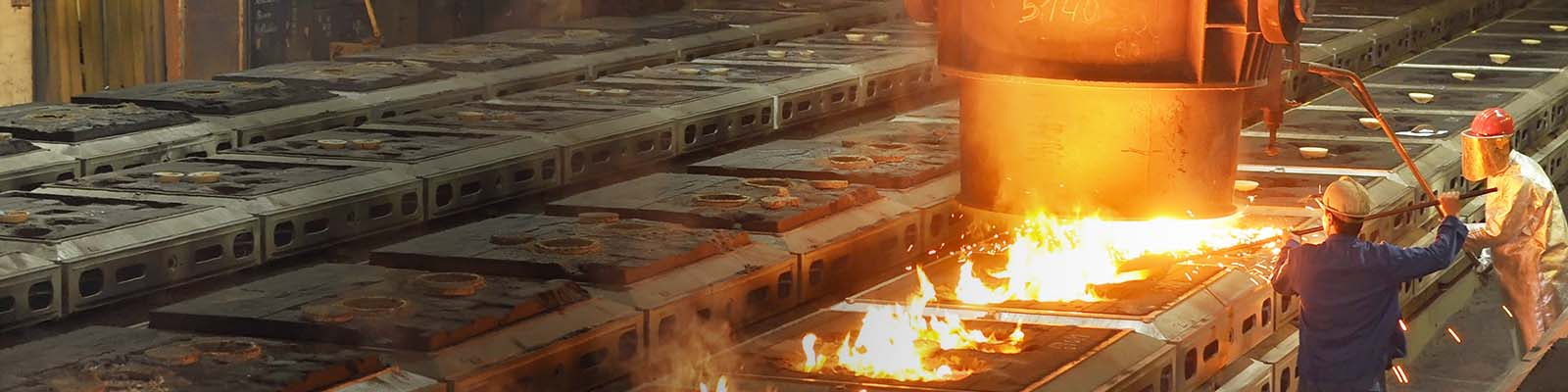
Step-by-Step Aluminum Spreading Process
Commencing the light weight aluminum casting procedure involves careful prep work and adherence to an accurate series of steps to make certain the production of top quality spreadings. The very first step is pattern creation, where a replica of the last product is made from metal, plastic, or timber. This pattern is then utilized to develop the mold, which can be made from products like sand or plaster. As soon as the mold and mildew is prepared, it is time to melt the light weight aluminum in a heater at temperatures surpassing 1200 ° F.
After getting to the wanted temperature level, the molten aluminum is poured right into the mold and mildew cavity. This step requires care and accuracy to stay clear of defects in the final casting. The light weight aluminum is left to strengthen and cool inside the mold before it is eliminated for completing. Post-processing methods such as grinding, fining sand, and warmth therapy might be utilized to accomplish the preferred shape, surface finish, and mechanical properties.
Throughout the entire process, careful surveillance and high quality control steps must be implemented to make certain the final aluminum spreading satisfies the called for requirements and standards.
Tips for Perfecting Your Spreading Technique
In refining your light weight aluminum casting strategy, careful attention to information and adherence to exact actions are vital to making sure the manufacturing of high-grade castings. One vital suggestion for perfecting your casting strategy is to thoroughly prepare the mold and mildew and ensure it is clean and effectively coated with a release representative to aid in the very easy removal of the casting. Additionally, preserving the light weight aluminum at the appropriate temperature level throughout the casting process is crucial for achieving optimum flow and minimizing the threat of problems. One more pointer is to pour the liquified light weight aluminum slowly and read this article progressively right into the mold and mildew to stop air entrapment and ensure a smooth fill. It is likewise vital to allow sufficient time for the aluminum to strengthen entirely prior to eliminating the spreading from the mold and mildew. Evaluating the spreading for any blemishes and making necessary adjustments to the procedure will assist you boost and best your light weight aluminum casting method over time.
Conclusion
To conclude, adhering to proper security preventative measures, establishing a suitable office, choosing the correct light weight aluminum alloy, and faithfully adhering to the step-by-step casting process are crucial for effective light weight aluminum spreading. By taking note of these essential variables and including suggestions to fine-tune your strategy, you can attain superb cause your light weight aluminum casting tasks.
From safety precautions to improving casting techniques, this handbook offers as a beacon of expertise for those venturing right into the globe of light weight aluminum casting.
Commencing the aluminum casting process entails precise preparation and adherence to a specific series of steps to guarantee the manufacturing of high-quality spreadings.In refining your aluminum casting method, thorough attention to detail and adherence to specific steps are extremely important to ensuring the production of top notch castings. One vital suggestion for developing your spreading technique is to very carefully prepare the mold and mildew and guarantee it is tidy and appropriately coated with a launch representative to aid in the very easy removal of the casting. Inspecting the casting for any flaws and making required Learn More Here adjustments to the process will certainly help you enhance and excellent your light weight aluminum spreading method over time.
Report this page